In the electronics industry, circuit boards (PCBs) are the backbone of almost every device we use today. From smartphones to medical devices, PCBs are responsible for making sure that these devices work as they should. However, the manufacturing process of PCBs is complicated, and even a tiny defect can cause huge problems in the end product. This is where functional testing comes into play. In this blog, we’ll explore what functional testing is, why it’s essential in PCB assembly, and how it ensures the reliability and performance of electronic devices.
What Is Functional Testing?
Functional testing is a form of testing conducted during the PCB assembly process to ensure that the assembled board functions as specified by its design parameters. In contrast with other modes of testing, for example, ICT or AOI, which screen for a specific component or aesthetic defects, functional testing tests the entire PCB. It works under simulated operating conditions to guarantee that the board functions as intended.
In other words, functional testing asks the question: Does the PCB perform its intended function? Functional testing is important because it guarantees that the end product will function as anticipated in its real-world application.
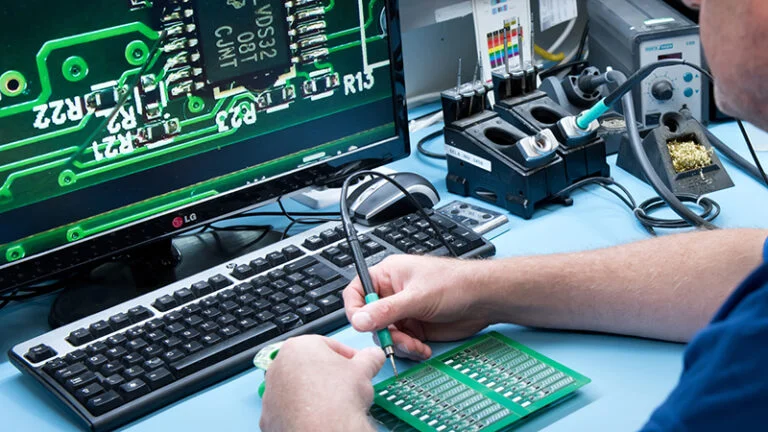
Why Is Functional Testing Important in PCB Assembly?
Functional testing is an important process in the PCB assembly process for several reasons:
1. Ensures Product Reliability
The main objective of functional testing is to verify that the PCB works as expected in actual operating conditions. Functional testing, through simulation of operating conditions, indicates if there is any problem that would influence the performance or reliability of the end product. This is particularly crucial where failure is not acceptable, such as in aerospace, automotive, and medical equipment.
2. Identifies Design and Assembly Flaws
Functional testing has the potential to reveal defects that are not discovered in other phases of testing. For instance, it can discover problems with component placement, soldering, or even design problems that can affect the board’s functionality. Catching these problems early on will save manufacturers from rework and product recalls
3. Enhances Customer Satisfaction
A functionally tested PCB is likely to work consistently in the hands of the end user. Not only does this minimize the chances of product failures, but it also increases customer satisfaction and confidence in the brand. In today’s competitive marketplace, providing high-quality products is crucial for upholding a strong reputation.
4. Reduces Time-to-Market
Although functional testing provides an additional process to the manufacturing process, it will end up saving time since problems are identified and fixed before the product hits the market. This prevents delays due to faulty products and makes the production cycle run more smoothly.
5. Compliance with Industry Standards
Numerous industries also have strict standards and regulations that products should comply with before they can be sold. Functional testing ensures that the PCB is in line with these standards to avoid possible legal or regulatory problems in the future.
How Is Functional Testing Conducted?
Functional testing includes a series of procedures aimed at testing the PCB’s functionality. Here’s an overview of how this process works:
1. Test Plan Development
Before testing, a comprehensive test plan is prepared. The test plan describes the particular tests that will be executed, the passing or failing requirements for each test, and the equipment to be utilized. The test plan generally relies on the design specifications and intended use of the PCB.
2. Test Fixture Setup
A test fixture or test jig connects the PCB to the test equipment. The fixture is made to suit the PCB’s design, making it simple and precise to test. The fixture holds the board firmly in place and provides all the connections required.
3. Power-Up and Initial Checks
Once the PCB is mounted in the test fixture, it is powered on and initial checks are made. Such checks could include ensuring that the board is being supplied with the right voltage, that all parts are adequately powered, and that there are no short circuits or open circuits.
4. Functional Test Execution
The actual functional tests are subsequently performed. The tests replicate the PCB’s actual operating environment and test its performance. For instance, if the PCB is a component of a communication device, the test could entail sending and receiving signals to verify that the board processes them properly.
5. Data Collection and Analysis
Throughout the testing procedure, measurements are taken, and data is gathered to ascertain if the PCB fulfils the requirements. The data can be measurements of voltage, current, signal level, and other factors. Any variation from the anticipated outcomes is recorded and checked.
6. Reporting and Debugging
Once the tests are finalized, a report is provided that captures the results. If there are issues, the PCB is shipped for debugging and rework. After the issues are addressed, the board can be put through further testing to ensure that the issues have been resolved.
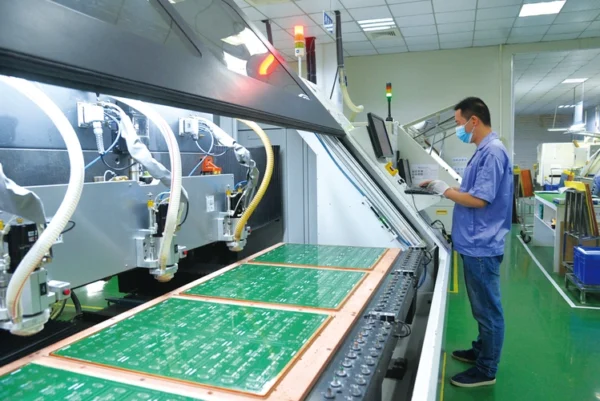
Types of Functional Testing
Various functional tests may be carried out on a PCB based on its application and design. Some of the most typical are:
1. Power-On Testing
It ensures that the PCB powers on appropriately and that all its components are receiving the proper voltage and current. It also confirms that there are no short circuits or power faults.
2. Signal Integrity Testing
Signal integrity testing tests the quality of electrical signals when transmitted through the PCB. It makes sure signals are not deformed or degraded, which may impact the performance of the board.
3. Communication Testing
For communication system PCBs, this testing ensures that the board is capable of transmitting and receiving data accurately. It could entail testing protocols like USB, Ethernet, or wireless communication.
4. Environmental Testing
Environmental testing tests the PCB’s performance under different environmental conditions, including temperature, humidity, and vibration. Environmental testing is especially critical for products that will be utilized in extreme or stressful environments.
5. Load Testing
Load testing tests the PCB’s capacity to carry its maximum anticipated load. This guarantees that the board can function reliably under peak loads without overheating or failure.
Challenges in Functional Testing
Though functional testing is crucial, it also has its drawbacks:
1. Complexity
The more complex the PCBs are, the more complex the functional tests must be to test them. Developing and executing detailed test plans may be time-consuming and involve expertise.
2. Cost
Functional testing involves the use of specialized equipment and fixtures, which are costly. Moreover, the testing itself can contribute to the total cost of production.
3. Time
Functional testing can be a lengthy exercise, particularly when problems are discovered and rework is necessary. Yet the effort put into testing frequently outweighs the gain in producing a product of which one can be certain.
4. Scalability
Scalability is a requirement for large-scale production, where functional testing needs to be able to handle high volumes of PCBs. This may necessitate automated test solutions, which can be expensive to implement.
Conclusion
Functional testing is a critical process in the PCB assembly lifecycle that confirms that the finished product fulfils its design requirements and functions well in real-world environments. Through the detection and rectification of faults at an early stage, functional testing enables manufacturers to provide top-grade products that fulfil customer demands and industry regulations.
At ESPCBA, I recognize the significance of functional testing in PCB assembly. Our experts are trained with the right knowledge and equipment to conduct thorough functional testing to ensure that your PCBs are efficient, reliable, and ready for use in any application. Whether you are creating a prototype or increasing production, we’re here to guide you through the process.
For further details regarding our PCB assembly and testing services, please visit our website at espcba.com. We can assist you in making your electronic designs a reality with confidence and accuracy.